6 Heat Sink Types: Which One is Best for Your Project?
Today we’ll talk about some different types of heat sinks, how they’re made, and their applications.
Generally, heat sinks are grouped by the manufacturing process used to create them, i.e. extruded, machined, etc. We will discuss 6 below. But, first, it’s important to understand that all heat sinks fall into two categories.
The Two Major Heat Sink Categories
All heat sinks can be broken down into two major categories… active and passive. What is the difference between active and passive heat sinks?
Active Heat Sinks
These generally have a fan or blower of some kind. The most common type is a ball bearing motor fan. These provide excellent performance, but they consist of moving parts and are on the expensive side.
Passive Heat Sinks
These have no mechanical components. They only use the convection process to dissipate thermal energy. Because they have no moving parts, they are more reliable. But they should still have continuous air flow across their fins.
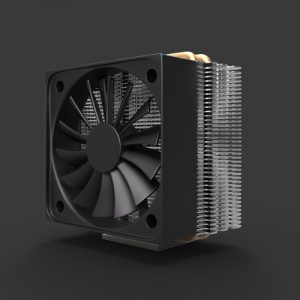
Example of an Active Heat Sink
Heat Sink Materials: Aluminum vs. Copper
Heat sinks are usually made from aluminum or copper. Each has its own advantages. Let’s talk about the main differences between them.
Aluminum Heat Sinks
Aluminum is the most common material for heat sinks. In particular, extruded aluminum heat sinks fit the needs of most projects. The metal is lightweight and has relatively good thermal conductivity.
Copper Heat Sinks
Copper has even better thermal conductivity than aluminum. It’s drawbacks, though, are weight and cost. The metal is sometimes used where the importance of thermal conductivity outweighs weight savings.
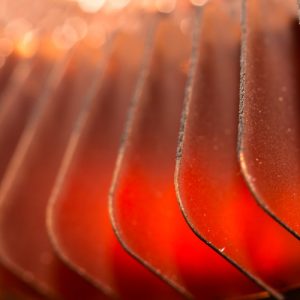
Copper Heat Sink Fins
6 Heat Sink Types (By Manufacturing Process)
Each heat sink manufacturing process has its own advantages and drawbacks. There are a number of different ways to make heat sinks. Let’s take a look at 6 common heat sink types.
#1 – Extruded Heat Sinks
The majority of heat sinks are made from extruded aluminum. The process is useful for most applications. Extruded heat sinks come at a low cost and custom specifications can be easily manufactured. The performance of extruded heat sinks can range from low to high. Their main downside, though, is that dimensions are limited by the maximum width of extrusion. Learn more
#2 – Bonded Heat Sinks
These are normally used for applications that require large-sized heat sinks. One benefit of these is that the base material and fin material can be different. Also, a combination of aluminum and copper fins can be used instead of just one fin material. This allows you to improve thermal performance while adding a minimal amount of weight. Bonded-fin heat sinks generally offer moderate performance and come at a high cost.
#3 – Skived Heat Sinks
Heat sinks produced through this method are normally made from copper. They are produced from a solid block of metal. These heat sinks offer high design flexibility and you can achieve high fin-density. This creates more surface area and opportunity for heat dissipation. They offer medium to high performance, but their drawbacks are generally high weight and directional sensitivity.
#4 – Stamped Heat Sinks
In this process, metal fins are stamped and then soldered onto the base. These are generally used for low-power applications. The advantage of stamped heat sinks is their very low cost due to ease of production automation. However, the biggest drawback is low performance.
#5 – Forged Heat Sinks
Forged heat sinks are made by compressing aluminum or copper and have many applications. Heat sinks can be cold forged or hot forged. These offer medium performance and can be made at low cost for high volumes. However, they offer limited design capabilities.
#6 – CNC Machined Heat Sinks
These offer high thermal conductivity, and you can achieve the most complex geometries with this process. This means you have plenty of flexibility in your design. But, they come at a high cost and the production time for each piece can make them less-than-ideal for high volumes.
Choose the Right Heat Sink Type for Your Needs
Heat sinks help absorb and dissipate the heat generated by electronic devices. You need to be sure you choose the appropriate type based on your design needs and volume requirements.
Remember that sometimes active heat sinks are required for enhanced heat dissipation. But passive heat sinks with no moving parts can be used as well.
Also, when it comes to materials, aluminum offers weight and cost savings, while copper allows the highest level of thermal conductivity.
From extrusion and bonding to forging and machining, there are a number of different manufacturing options available. Each has its advantages and drawbacks.
If aluminum extrusion or CNC machining happen to fit your needs, we can help.
Learn more about our high-quality Asian manufacturing services below.