Aluminum is the material of choice for many designers because it works well in such a wide range of applications. You can customize your aluminum extrusions by incorporating different alloys, surface treatments, and coatings to suit your project’s needs.
Making these selections lets you alter the aluminum’s strength, ductility, corrosion resistance, and visual appeal. But another way to get the most out of your aluminum parts is by using tempers to hone specific characteristics.
Here we talk about the different alloy series — essential background information — and then we discuss how tempering works and how to choose the right temper for your aluminum part.
Table of Contents
An Overview of Aluminum Alloy Designations
Before you can understand tempers, it’s essential that you first understand aluminum alloying.
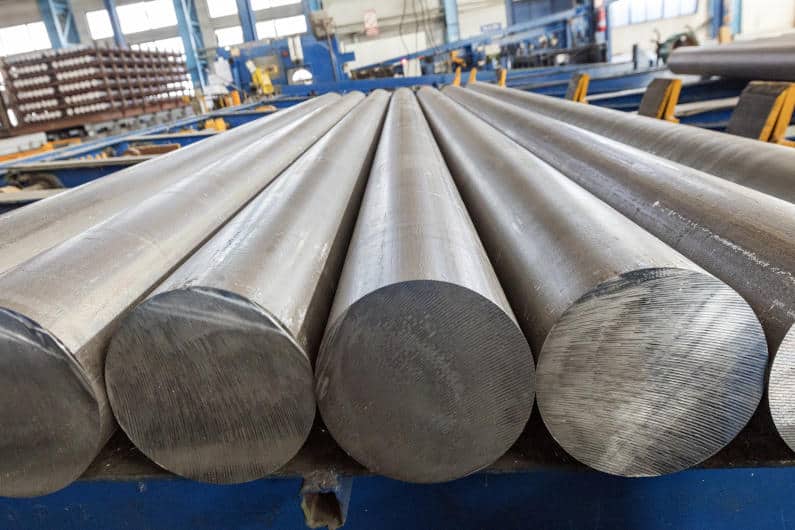
Aluminum billets used for the extrusion process
Aluminum alloys are designated as different grades based on a 4-digit identifier (e.g., aluminum alloy 6063). The first digit in this alloy number identifies its series — aluminum alloys are categorized into different series based on their main alloying elements.
The listed wrought aluminum series below state the main element(s) in the alloy (other than aluminum):
- 1XXX – contains 99% or more aluminum
- 2XXX – alloying element is copper
- 3XXX – alloying element is manganese
- 4XXX – alloying element is silicon
- 5XXX – alloying element is magnesium
- 6XXX – alloying elements are silicon and magnesium
- 7XXX – alloying element is zinc
- 8XXX – another alloying element besides those listed above
Each of the above series has different properties, and different chemical compositions within the series lead to an even wider range of properties. Alloys in the 6XXX series, for example, are often the first choice for structural and architectural applications that require strong aluminum extrusions with higher corrosion resistance.
However, the properties of an individual alloy can be honed even further with a suitable temper.
Mind Your Temper – This is How Aluminum Tempers Work
Tempers are used to refine aluminum alloys to promote certain physical properties. This can include improved strength, improved ductility, improved corrosion resistance, improved hardness, and more. There are five main temper designations which are added as a suffix to the alloy identifier:
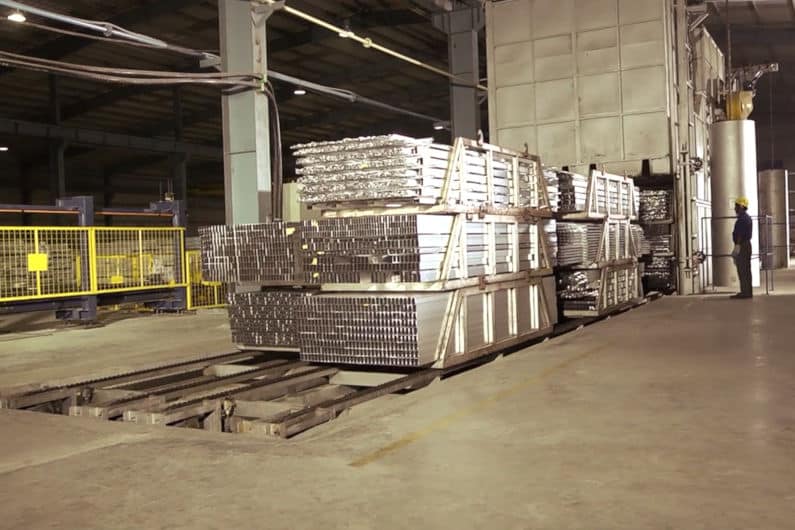
Aluminum extrusions going into an aging oven
F – As Fabricated means that no special thermal or mechanical controls were used during production, which often applies to products that will be further refined.
O – Annealed means a heat treatment was used to remove all strain hardening, effectively “relaxing” the microstructure, producing a low strength, highly ductile microstructure.
H – Strain Hardened means the microstructure was strengthened using cold working, which requires the application of stress to the metal at relatively low manufacturing temperatures (room temperature), such as by cold rolling.
W – Solution Heat Treated means unwanted precipitates were removed by heating and then rapid cooling. Solution heat treatment is often an intermediate processing step, not the final product.
T – Thermally Treated means heating, aging, and controlled cooling are used to strengthen the microstructure.
Strain hardened (H) and thermally treated (T) temper designations are further subdivided with the addition of a number, which denotes how a temper is applied. For example, an H2 temper involves strain hardening followed by partial annealing, while a T6 temper includes solution heat treating followed by artificial aging.
How do You Choose the Right Temper?
First, consider that certain aluminum alloy series can only be strain hardened or thermally treated, which may limit the number of choices you have in manufacturing. Wrought aluminum alloys 1XXX, 3XXX, and 5XXX non-heat-treatable, while alloys 2XXX, 6XXX, and 7XXX are heat treatable. Some 4XXX series wrought aluminum alloys are heat treatable, while others are not.
Depending on the equipment you need for processing or the exact properties you want for the final product, some tempers will be better than others. We recommend reaching out to your extrusion manufacturer to get a list of the alloys and tempers available. They should be able to provide information about the characteristics of each alloy and temper combination.
When you are designing aluminum extrusions for your project, you need to think about more than just alloy and temper. You should also consider how to design your profiles for manufacturability. To learn more about how to do this, we recommend our aluminum extrusion design guide.