From rails for industrial equipment to automotive applications to bold artistic sculptures and architectural designs, there are plenty of reasons you may want to create curved aluminum extrusions.
While the ductility of aluminum makes it well-suited to bending for these applications, you must address several challenges to ensure your final product meets quality specifications. This decision-making process ultimately comes down to managing stresses during bending.
Bending aluminum extrusions imparts immense stress onto the workpiece. The extrusion can experience tension, compression, and torsion all at once. The results can range from minor thinning and swelling of profile segments to unacceptable defects like deformed profiles, buckling, or cracking.
This article explains some of the best practices extrusion designers can apply to ensure good bendability in their products, along with six popular methods for bending aluminum extrusions.
Table of Contents
Design Considerations for Aluminum Extrusion Bending
Designers that want to bend aluminum extrusions have a lot to consider. While some bending methods can achieve a tighter bend radius and others can better ensure profile stability, a few key considerations can help you improve your product’s bendability for any bending method.
Choice of Material
First, the material you choose has a major impact on bendability. As we’ve discussed in previous articles, some alloys are better suited to bending than others. While not the easiest to bend, alloys from the 6XXX series tend to see widespread application thanks to their exceptional combination of properties.
Bending Before Temper Treatment
The physical properties of an alloy can also be improved using temper treatments, but applying them before bending can make bending an aluminum extrusion more difficult and more expensive to produce. The simple workaround is to conduct the full or partial temper treatment after bending so that your product is cheaper to produce and better meets specifications.
Profile Design Choices
Other considerations for improving the quality of curved aluminum extrusions and lowering production costs can include:
- Improving profile geometry,
- Designing uniform wall thickness, and
- Minimizing the profile size when possible.
Especially with profile shape, poor design can lead to distortion of the profile and cracking during bending. Rounded corners, profile symmetry, and good internal supports can all help improve stability during bending.
Perform Surface Finishing Operations After Bending
Finally, if an extrusion bend design requires surface finishing, such as anodizing, or other secondary operations, it may be best to perform these operations after bending. While some surface finishes, like powder coating, may be capable of tolerating limited bending, there is always a risk that the bending process damages the surface.
While applying the considerations above can improve bendability and lower cost, they may not be possible depending on the restrictions of the design. Luckily, you still have options. If you have a difficult-to-bend aluminum extrusion, you can consult an experienced bending specialist to determine what additional measures you can take to meet your bending needs or if special equipment is needed.
How to Bend Extruded Aluminum: 6 Methods
There are several common ways to bend extruded aluminum which can be categorized into six main methods.
1) Roller Bending
As one of the most widely used methods for bending long aluminum extrusions, three-roller bending offers minimal tooling costs for common profiles and can roll fully circular components. While a key benefit of roller bending is that you can bend the entire extrusion length instead of only a single segment at a time, rolling for tighter bends may need to be done in increments to reduce the bend radius down to the desired curvature gradually.
The consequences of this stepwise rolling can include lower precision than other methods and poor scalability. These restrictions typically make roller bending better suited to low-to-medium size production runs and ideal for prototyping.
2) Ram Bending
Also known as push bending, this method is sometimes considered the simplest and least expensive approach, making it comparable to compression bending. While it can reliably bend extrusions to precise angles, ram bending is more likely than most other methods to deform the profile in undesirable ways and can only bend one portion at a time.
3) Rotary Draw Bending
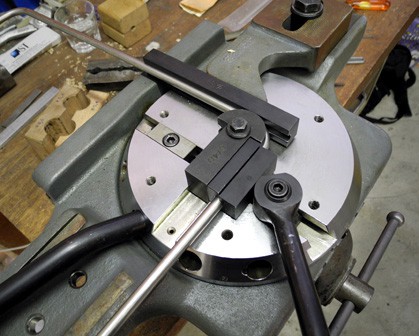
Image Source: Kolb-Rahmenbau.ch on Flickr
Rotary draw bending involves clamping an extrusion and pulling it around a rotating bending die. While capable of bending to exceptionally precise angles, rotary draw bending can only bend a single segment at a time.
Rotary draw bending also boasts the ability to handle larger-sized extrusion profiles and multiple, close-proximity bends in a single part. It is an ideal method for custom bending profiles on round tubing, which can be supported by an internal mandrel to provide extra support for the profile during the bending.
4) Compression Bending
While the basic setup looks similar to rotary draw bending, the process is less complicated. Instead of a rotating die pulling the extrusion around its perimeter, compression bending uses a compression die to wrap the extrusion around the fixed bending die.
Like rotary draw bending, you can bend only one section at a time and make multiple bends in any direction. However, this method offers the aluminum profile much less support and can easily result in deformation. The main advantage of compression bending is for high production volumes as it is fast and cost-effective to complete each bend.
5) Stretch Bending
Sometimes called tensile bending, stretch bending can be one of the more expensive bending solutions thanks to bending die costs, but it offers unique benefits. The bending specialist can achieve the desired bending shape with minimal distortion or surface damage by placing the workpiece in constant tension during bending.
While limited to larger bend radii, the bending die for this specialty method can achieve a range of dynamic shapes on very large workpieces. Larger production volumes using the same profile can help offset the cost impact of a stretch bending die.
6) Free-Form Bending
As one of the most advanced methods on this list, CNC free-form bending feeds the aluminum extrusion through an articulating ceramic die to form a wide range of complex custom bends. While most common for round tubing, this technique can form other extrusion profiles into unique products. This technology is less common than the other bending methods but may see significant potential in the near future.
Which Method is Best for Your Product?
Each bending method has unique advantages that make it better suited to specific applications. While ram bending and compression bending offer low-cost options for bending aluminum extrusions, they can negatively impact aesthetics and sturdiness. On the other hand, stretch bending and rotary draw bending can produce high quality, high precision bends, but at higher costs and with other potential drawbacks.
Overall, even with the best bending method for your product, consistently meeting quality requirements for challenging extrusion profiles may prove extremely difficult. To help with this, consult our Extrusion Design Guide or speak with a Gabrian service professional to get expert insight into designing and bending extruded aluminum products.
Get the best value out of your next aluminum extrusion project by partnering with Gabrian. Our Custom Aluminum Extrusion Services will help you meet your project requirements while keeping production costs low.