Aluminum Extrusions for Photovoltaics: An Overview
The United States is forecast to install nearly 100 gigawatts of new solar power capacity within the next five years, a growth rate of 42%. And the worldwide market for installed solar is projected to surpass $200B by 2027.
This installed base will be split between large-scale solar farms, residential and commercial rooftops and a smaller amount in car- and truck-top mobile solar panels.
In all these applications, however, the success of photovoltaics relies on using aluminum architectural components for both fixed and moving structures.
Here, we discuss the benefits and drawbacks of aluminum for applications in the solar power industry as well as some design considerations for framing systems.
Table of Contents
Aluminum vs. Steel for Solar Panel Frames
Traditionally steel has been the metal of choice for large-scale commercial projects, and there are good reasons for this.
Steel is abundant and easily sourced. Steel is great for static load bearing, with a high modulus of elasticity and excellent fatigue strength. The mechanical and forming properties of steel are well understood and so the design of structural members like frames, trusses and I-beams is relatively straightforward.
But there are also notable drawbacks to the use of steel. It is heavy, for one, and must be carted and installed in remote locations at a high energy cost.
Making longer steel sections requires joining pieces together via welding, an additional manufacturing expense. And of course, steel easily corrodes so the surface must be passivated, painted or powder-coated – none of which is a permanent solution to longevity.
Luckily there are advantages to the use of aluminum extrusions that many engineers and product developers may not be aware of. To exploit those advantages, engineers should first be mindful of the exact conditions under which the structure must perform.
Design Considerations for Aluminum Frames
Before considering aluminum extrusions, there should be a clear understanding of the stresses that the structure will need to withstand.
Mitigating factors include snow loads, heavy winds and large temperature variations between day and night. Is the structure intended to be fixed or moving? Will it potentially be exposed to saltwater spray or other environmental contaminants?
All of these challenges can be overcome with careful design and the use of the right alloys. Here are just some of the benefits of the use of aluminum extrusion for solar panel installations.
The Benefits of Aluminum Extrusions
First, aluminum profiles are virtually limitless in design complexity. This means that any likely engineering requirement can be met by tailoring the profile to suit the exact performance requirements.
Secondly, aluminum is naturally corrosion resistant and forms a hard aluminum oxide layer when exposed to oxygen which helps to deter further corrosion. Aluminum can be anodized to add additional protection while enhancing its aesthetic appeal.
Thirdly, the lighter weight of aluminum makes it ideal for moveable assemblies that must track the sun across the sky. This is also a clear advantage for rooftop and car top panel mounts.
Finally, extrusions are ideal for modular installations that can be easily connected with fasteners that allow for the necessary thermal expansion and contraction of heating and cooling cycles.
What Are The Drawbacks?
By unit weight, aluminum is a more expensive material than steel, and there is usually more design work involved at the initial stage.
However, studies conclusively show that these upfront costs more than pay for themselves in the long term through better performance, lower installation costs and enhanced longevity.
Choosing an Aluminum Alloy
What is the best type of aluminum? There is no perfect answer, so again that depends on the application.
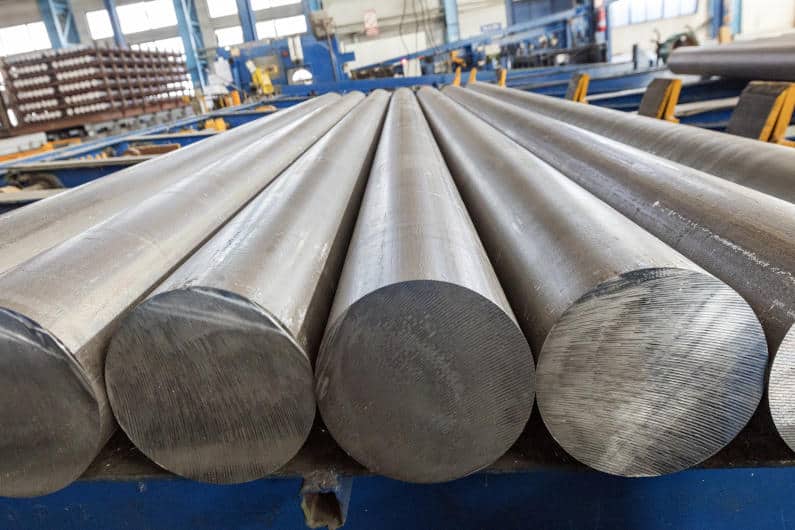
Aluminum billets used for the extrusion process
But there are several good choices readily available:
- Aluminum 6063: This alloy is the least expensive and also has the lowest ultimate strength. But it’s also easy to extrude and has the best surface finish. The chemical and mechanical properties of 6063 are well understood and it’s the alloy of choice for later anodizing.
- Aluminum 6061: Slightly higher cost and higher strength than 6063, but more difficult to extrude.
- Aluminum 6005A: This is one of the newer alloys with many beneficial properties. It is light, strong, easy to extrude, and produces an excellent surface finish. This is probably the best choice for solar cell applications.
To get the most benefit from the extrusion process, engineers need to adhere to good design principles. Maintain consistent wall thicknesses and avoid abrupt changes in thickness in adjoining areas; keep profiles symmetrical whenever possible; avoid sharp corners and recesses; use small tongue ratios.
Because of the unique characteristics of the extrusion process, developers are well-advised to work closely with the manufacturer to optimize their designs for manufacturing. If you have questions about how aluminum extrusions can benefit you, the experts at Gabrian are standing by to offer professional expertise. Contact us today.