When thinking of strong materials, either for a project or in general conversation, aluminum isn’t typically the first material to pop into people’s minds. Many relate aluminum with kitchen foil, beverage cans, and foldable furniture — products that are not exactly the embodiment of strength.
On the other hand, steel is very likely to be top of mind if you’re searching for a strong material. After all, prison bars, car frames, building support beams, and ships are made primarily of steel.
Is the difference in strength between these two materials that big? Are they comparable in the strength category? In this article, we will try to show that our conceptions regarding the strength of these two materials might not be completely accurate.
Table of Contents
What is Strength? Different Types of Strength Measurements in Materials
It’s hard to compare the strength of these materials if we don’t first agree on what “strength” means.
A simplified definition of a material’s strength is its ability to withstand a certain amount of load, also known as force or stress, before it reaches specific points of deformation or strain. A typical way of visualizing this is by the well-known stress-strain curve, shown in the example below.
These curves are typically made by using a sample of material, such as aluminum, and applying tensile force to cause deformation up until the point of rupture. The stress, and therefore the strength of the material, is usually measured in units of megapascals (MPa) or kilopounds per square inch (ksi). Deformation is measured as a percentage of the original length of the sample.
Yield Strength vs. Ultimate Strength
The stress-strain curve in the figure above shows two very important points: yield strength and ultimate strength.
Yield strength refers to the maximum amount of load that the material can withstand before suffering plastic (permanent) deformation. Up until this point, all the deformation that the material suffers can be reversed if the load is removed. Think of this like a rubber band that, when you stretch it, deforms without reaching its yield point because if you stop applying force, it comes back to its original form.
Ultimate strength, on the other hand, is the maximum stress a material can withstand before failure, or rupture. All the deformation that occurs between the yield strength and maximum strength is plastic deformation.
This stress-strain test can be drawn using different types of applied forces. The most common is performed by applying tensile strength, which is to say, by pulling the material apart. By doing this test, we can determine the ultimate tensile strength of a material, which is the most common metric by which strength is compared.
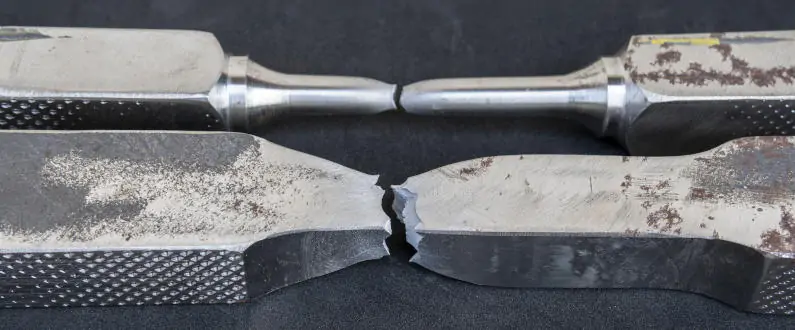
Metal that has undergone tensile testing, which involved pulling it for a short time at a constant rate.
Other types of loads that can be applied to materials to test their strength are compression, torsion, impact, and shearing.
Different Aluminum Grade, Different Strength
The ultimate tensile strength of aluminum is a highly variable characteristic. This is because aluminum comes in many different grades depending on the alloying elements that are used and in what amounts, each of which has a different impact on strength.
Although some aluminum grades are not at all strong, such as pure aluminum, which is a relatively soft metal, some of its alloys can achieve considerable strength.
Learn More About Aluminum Grades
Is Aluminum Strong Compared to Steel?
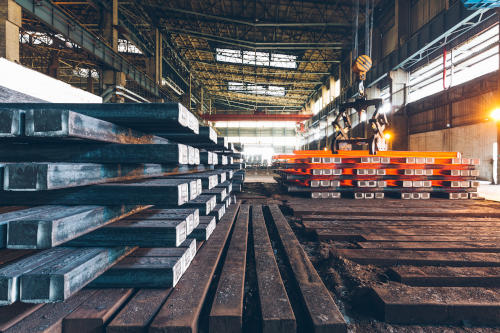
Inside a steel manufacturing facility
Many aluminum grades can be considered of very high strength, even comparable to some steels. Nevertheless, comparing samples of the same size of the strongest aluminum alloys and steel alloys, more often than not, steel will be the strongest.
As an example, the maximum tensile strength of one of the commonly-found strongest aluminum alloys, the AA7068-T6, and one of the strongest steel alloys, the AISI 1080, are 710MPa and 965MPa, respectively. Here you can see a comparison of their Yield Strength and Ultimate Tensile Strength.
However, if you compare strength-to-weight ratios, which is to say, you consider how much strength each material brings to the table by weight, aluminum alloys get much closer to steel than you would probably imagine. In some cases, they even outperform steel.
This shows that strength alone is not a great measure when choosing a material. If you want a very strong material but are limited by weight, aluminum may be a better choice, or if you’re limited mainly by space, steel could probably take the advantage.
If you would like to read a more in-depth comparison between steel and aluminum that takes more properties into account than only strength, check out our Steel vs. Aluminum article.
The Strongest Aluminum Alloys and Their Applications
The following table shows some of the strongest commonly used aluminum alloys. Some of these have already replaced steel in specific applications since they provide sufficient strength for that purpose but also provide some advantages that steel cannot, such as low relative weight and improved corrosion resistance.
Conclusion: Don’t Look at Strength in a Vacuum
Seen in a vacuum and by volume, steel is normally considerably stronger than aluminum. Nevertheless, strength is just one of the many properties that have to be considered when choosing a material for a project, and aluminum has many characteristics that make it a fair contender together with steel.
If you would like to learn more about the different grades of aluminum alloys and which would be best suited for your project, take a look at our Aluminum Grades article.