Smart Ways to Reduce PCB Assembly Costs
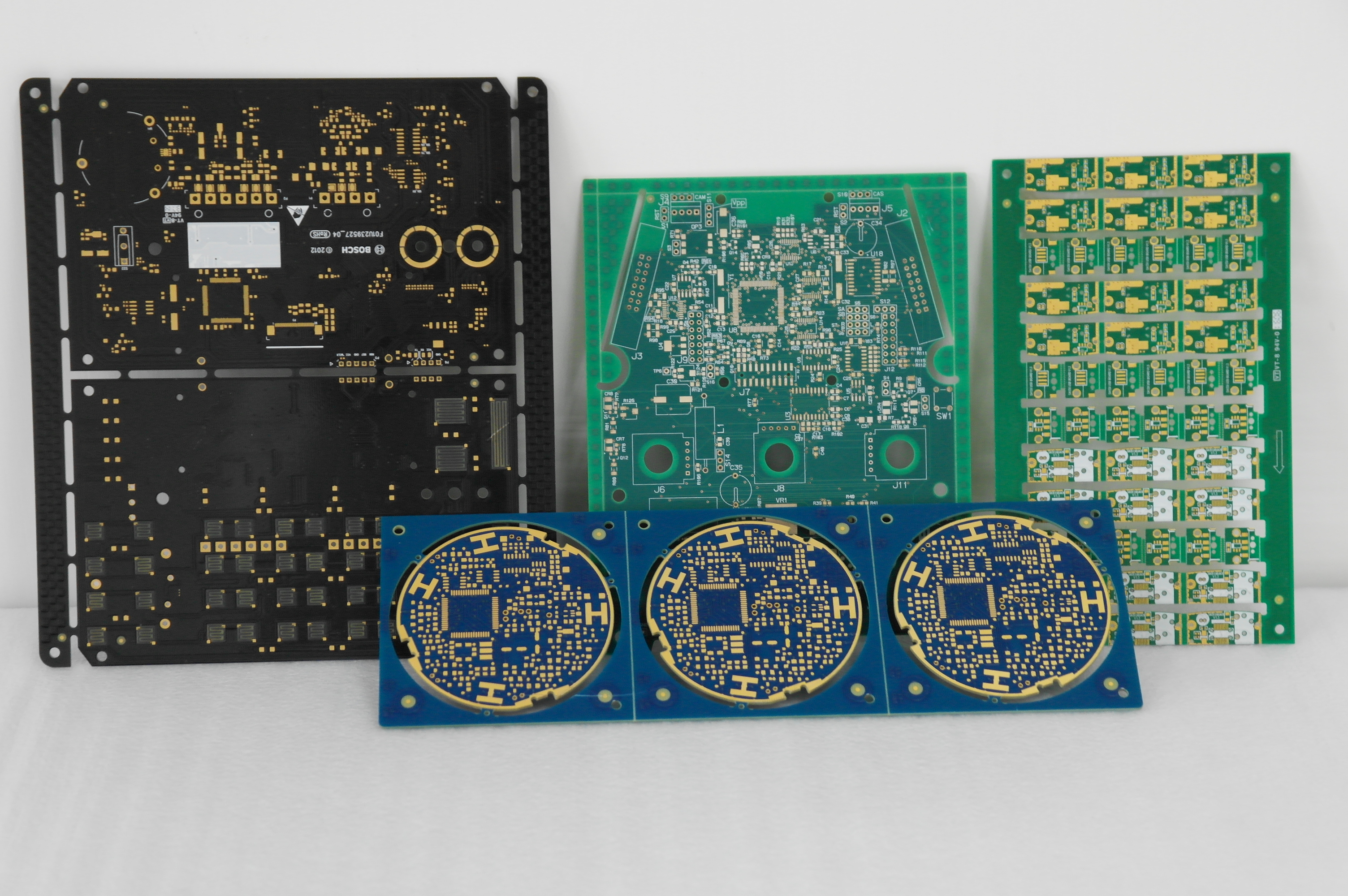
How to Reduce the Total Cost of Your PCB Assembly Project
One of the key ways procurement departments contribute to their organization financially is by reducing the total cost of the purchases they make. When it comes to reducing the cost of a PCB Assembly project, there are some steps you can take that not every company considers.
We spoke with Bob Lockhart, a procurement veteran and one of the founders of Gabrian International. We wanted to get his ideas on how to reduce the costs of a PCBA project. Below are the 3 important tips Bob shared with us.
3 Smart Tips for PCB Assembly Cost Reduction
#1: Provide multiple component sources for each component.
#2: Keep panelization flexible and optimized to the needs of the PCBA manufacturer.
#3: Provide a fast track process to qualify lower cost sources between Design Engineering and Purchasing.
Cost Reduction Tip #1:
“Provide Multiple Component Sources for Each Component.”
You should avoid single sourcing wherever possible. Why?
There are several key advantages. For example, with multiple component options, you have a greater availability of parts in distribution. You also have component cost leverage. And if there are quality issues with parts, you can select another source immediately.
The biggest problem with single sourcing? You could end up not being able to manufacture the product because parts need to be ordered from the factory and lead times can be significant.
Cost Reduction Tip #2:
“Keep Panelization Flexible to your manufacturer’s needs.”
You want to make sure that panelization is optimized to the needs of the PCBA manufacturer. Let’s take a look at an example:
Here is a 6-up panel, meaning the panel makes 6 PCBAs at a time. Note the 4 mounting holes (.127 dia) in the corners. This is how the PCBs are mounted in the assembly equipment. If a factory has fixtures designed for processing 6.5 x 4.25 panels with .127 pins for mounting this will work well for them.
But a company that uses .250 pins would prefer panels that are 12-up rather than 6-up. It is cheaper to conform with the equipment of the factory you are working with than to maintain your original designs.
Cost Reduction Tip #3:
“Qualify Lower Cost Sources More Quickly.”
Set up a process to qualify lower cost sources between your Design Engineering and Purchasing departments. This is easier said than done. Conflicting priorities between Design Engineering and Purchasing can impede the process.
One solution is to set up Material Cost Reduction Committees. Management partners up with Purchasing and Engineering to identify high-value cost reduction opportunities. They also work to determine strategic components that need multiple sources to assure continuous production.
Use These Tips to Reduce the Total Cost of Your PCBA Project
Armed with these tips you’ll be able to reduce your PCB Assembly costs by optimizing component sourcing, fast-tracking low-cost sources, and keeping your panelization flexible.
Always Ask PCB Manufacturers These 7 Important Questions Before You Work With Them
In this free white paper, we’ve drawn on our experience to create a checklist that will help you make your search easier.