When thinking about the best metal for a project, it’s natural to think that strength is the most important physical property. After all, the stronger a material is, the better, right?
In reality, metals and their properties are much more nuanced than that. Although strength is a top design consideration, many other physical properties can be important. One of those is called ductility.
This article explores what ductility is and how it can be beneficial for certain aluminum applications.
Table of Contents
What is Ductility?
Ductility measures how much a material can be pulled apart from two ends without breaking.
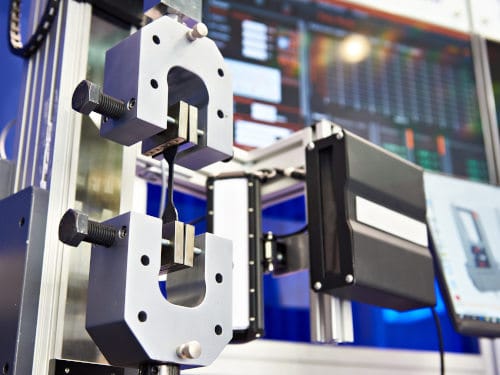
A tensile testing machine
We can tensile test a sample of material using equipment as you see above. Once the material is tested to failure (rupture), we quantify its ductility as the percent elongation or percent reduction in area.
In our aluminum strength article, we presented the figure of a stress-strain curve. We mentioned that the deformation between the yield and rupture points is called plastic, or permanent, deformation.
In highly ductile materials, these two points are far apart from each other along the strain axis. You can see this illustrated in blue below.
In brittle materials, these two points are very close to each other. These materials demonstrate less strain between the start of permanent deformation and ultimate failure.
Highly ductile materials subjected to tensile stress will suffer considerable plastic deformation before fracturing, which allows them to become very thin and drawn. Brittle materials, such as a piece of glass subjected to the same tensile stresses, will fracture before permanently deforming.
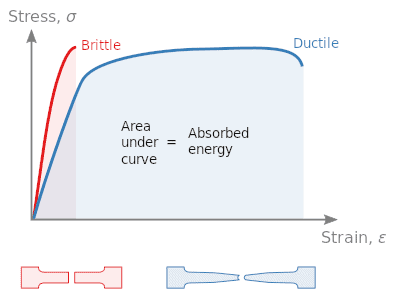
Source: Wikimedia Commons
Highly ductile materials subjected to tensile stress will suffer considerable plastic deformation before fracturing, which allows them to become very thin and drawn. Brittle materials, such as a piece of glass subjected to the same tensile stresses, will fracture before permanently deforming.
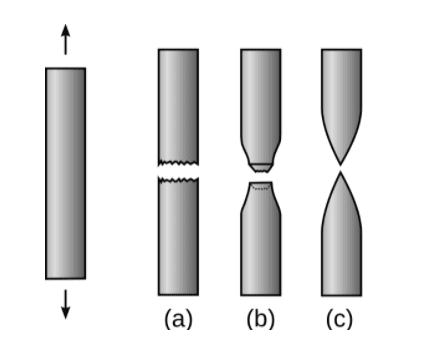
Source: Wikimedia Commons
The three materials you see above have been submitted to a tensile force (pulled apart).
- Material (a) is brittle and breaks without any plastic deformation
- Material (b) goes through some plastic deformation
- Material (c) is highly ductile and suffers considerable deformation before fracture.
You can see that material (a) is the most brittle and material (c) is the most ductile.
Ductility in Aluminum and Other Metals
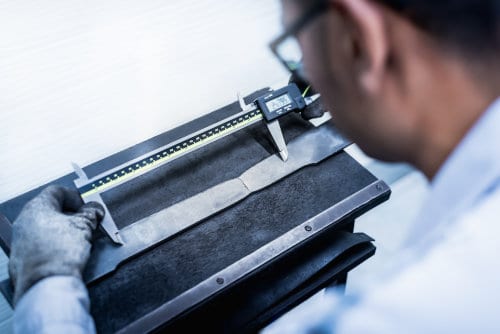
Engineer using digital vernier to measure the elongation of a material
Generally speaking, all metals can become ductile when you apply heat to them. At room temperature, however, different metals have varying levels of ductility.
Gold, platinum, and silver are very ductile, and you can draw them into thin wires. On the other hand, silicon, boron, and germanium are some of the most brittle metals. Impure or hardened alloys such as tungsten carbides and cast iron are also quite brittle.
Pure aluminum has high ductility, but adding other elements to create aluminum alloys negatively affects it. Nevertheless, most aluminum alloys still retain a moderate degree of ductility.
Aluminum Ductility Examples
This section provides a comparison between the ductilities of some different aluminum alloys used for extrusion, as well as some other popular manufacturing metals. You can use these benchmarks to gauge how ductile or brittle certain aluminum alloys are.
It’s interesting to note that the same aluminum alloy will have a dramatically different ductility depending on its heat treatment. This is because, relative to the annealed condition, different heat treatments generally increase the hardness of the aluminum, which decreases ductility.
Advantages of Aluminum’s Ductility
Aluminum’s ductility gives it an essential advantage in structural applications. When structural beams or suspension cables receive stress above their yield stress level, they absorb some applied energy without breaking. This way, there is an opportunity to identify and fix the over-stressed parts before catastrophic failure and public injury occur.
Improved formability is another crucial advantage of aluminum’s ductility. You can draw it into thin wires and form it into other shapes at lower temperatures than brittle metals.
For example, stamping and extruding are forming processes that pair well with highly ductile metals such as aluminum. This increases the variety and complexity of shapes it can form and makes manufacturing aluminum products more cost-effective.
Conclusion
The ductility of a metal might not always be considered a top priority when choosing the best material for a project. However, it’s an advantageous physical property to have in many applications.
Aluminum and its alloys exhibit a wide range of ductilities, from moderate to very good. They are well suited to accommodating lightweight structural applications. For example, the ability to remain strong and flex without breaking is uniquely essential for applications like the structure of airplane wings and bicycle frames.
The ductility of aluminum is also crucial for specific structural applications such as home furniture and ladders, which are more easily formed and more lightweight than steel. If you’re interested in seeing how aluminum compares in other physical aspects to steel, check the following article, which compares the two metals: